The automotive industry requires high precision, with thousands of components of different sizes and shapes. Vibrating feeders help automate the feeding process, ensuring speed, accuracy and efficiency.
This article SWOER will delve into the role and benefits of custom vibrating feeders in the automotive industry, and give you a detailed look at practical applications.
Challenges in automotive component supply
Modern automotive assembly lines require precision, speed and efficiency. Feeding components into these lines also presents significant challenges, particularly due to:
Diversity of components
- Size: From small screws to large engines and chassis.
- Shape: Various – round, hexagonal, square, asymmetrical.
- Material: Metal (steel, aluminum, copper, ...), plastic, rubber, ... each type affects the way of feeding.
Accuracy requirements
- Location: Components must arrive at the correct assembly position, without deviation.
- Direction: Precise orientation to ensure perfect fit.
- Small mistake: May cause assembly errors, affecting vehicle quality and safety.
High productivity
- Mass production: High feeding speed to meet large output.
- Minimize downtime: Minimize interruptions to ensure continuous operation of the line.
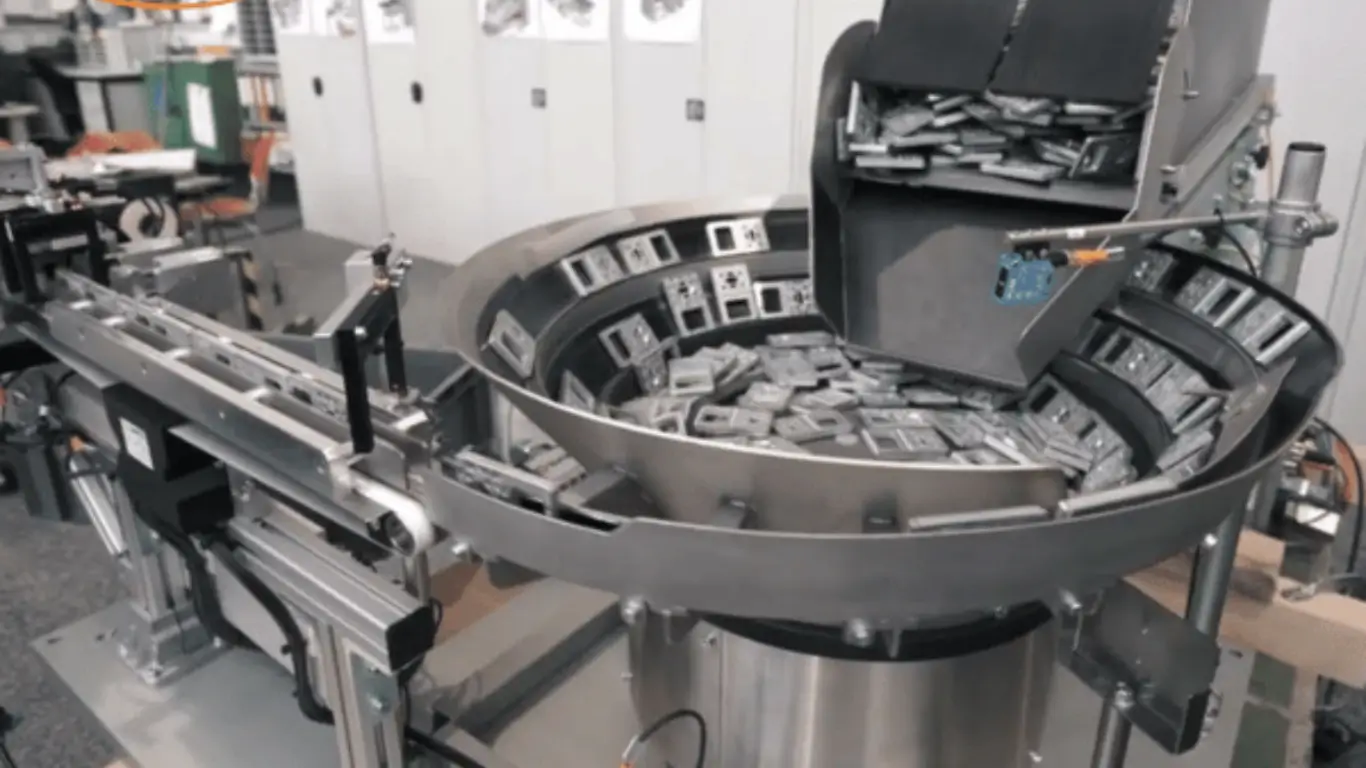
Customized Vibrating Feeder – The Ultimate Solution for the Automotive Industry
In the automotive industry, with the diversity and complexity of components, the use of customized vibrating feeders is becoming the optimal solution to meet the specific requirements of each production line.
So what is a custom vibrating feeder?
Unlike standard vibrating feeders, custom vibrating feeders are specifically designed to meet specific component types, productivity, accuracy and environmental conditions.
Outstanding advantages:
Flexible design:
- Shape and size: Vibrating funnels, guides, and traps are designed to suit the shape, size, and characteristics of each type of component (bolts, screws, nuts, bearings, etc.).
- Materials: Manufacturing materials are selected based on requirements for durability, abrasion resistance, anti-static, etc.
Improve productivity:
- High Speed: Meet mass production needs with high feeding speed.
- Stability: Stable, continuous operation, minimizing line downtime.
Improve quality:
- Accurate: Ensures accurate component orientation and feeding, in the correct position and direction.
- Minimize errors: Limit errors, assembly errors, improve product quality.
Cost savings:
- Reduce Labor: Automate the feeding process, reducing dependence on manual labor.
- Reduce scrap: Precise material feeding helps reduce scrap and waste of raw materials.
Specific applications in automobile manufacturing
Custom vibrating feeders play an important role in the automation of automotive production lines, ensuring high precision, speed and efficiency in the assembly process. Here are some specific applications:
- Engine assembly: Feeding bolts, screws, pistons, piston rings, etc. with high precision and fast feeding speed, ensuring uniformity and stability.
- Body assembly: Feeding welding parts, bolts, rivets, etc. with the ability to handle components of various sizes and shapes, ensuring positioning accuracy.
- Electrical system assembly: Feed connectors, wires, sensors, etc. with anti-static design, helping to protect small and sensitive components.
- Furniture assembly: Feeding small parts such as buttons, screws, etc. at high speed, ensuring accuracy and aesthetics.
- Other applications: Support the assembly of gearboxes, suspension systems, brake systems, etc. with optimal performance.
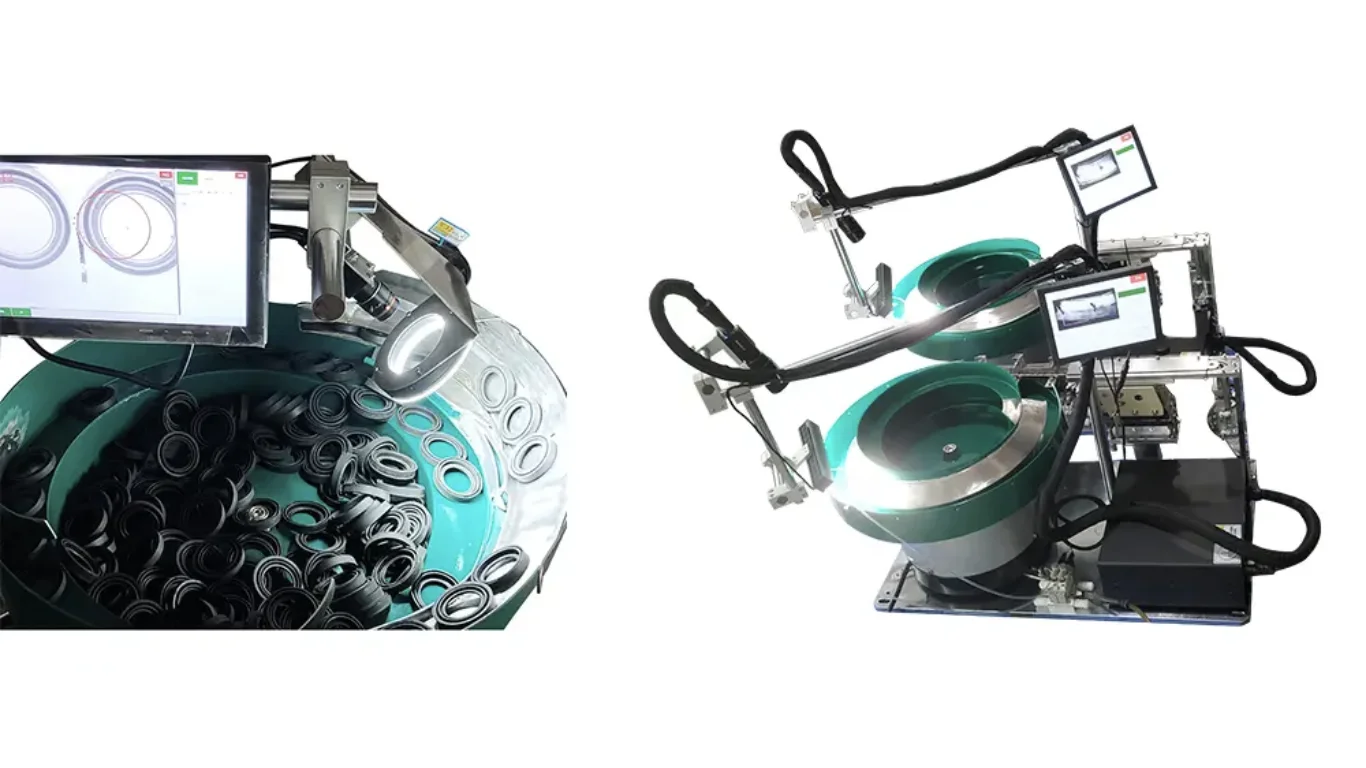
Benefits of Using Custom Vibrating Feeders in Automotive Manufacturing
The application of customized vibrating feeders brings many practical benefits to automobile manufacturing enterprises, contributing to improving production efficiency, improving product quality and enhancing market competitiveness.
Increase productivity and production efficiency
- High feed rate: The machine is designed to meet mass production with fast feeding speed, helping to increase assembly productivity.
- Reduce downtime: Stable and continuous operation, limited interruption, ensuring production progress.
- Process Optimization: Automation helps improve operational efficiency and reduce dependence on human labor.
Improve product quality, reduce defect rate
- High precision: Precise orientation and feeding, ensuring components are in the correct position and direction, minimizing errors.
- Quality control: Some machines integrate a testing system, remove defective components, ensuring the quality of output products.
- Reduce error rate: Thanks to automation, it helps to reduce assembly errors and enhance brand reputation.
Save cost, labor, time
- Reduce labor costs: Automation helps reduce the number of workers, optimizing operating costs.
- Reduce waste: Precise material feeding helps reduce material waste.
- Save time: Shorten assembly time, increase production efficiency.
Ensure labor safety
- Risk Reduction: Limit worker exposure to small parts and machinery, reducing the risk of accidents.
- Improve the working environment: Reduce noise, dust, create a safer working environment.
Increase competitiveness for businesses
- Improve production capacity: Respond to market demand quickly with large output.
- Improve product quality: Increase brand reputation, attract customers.
- Reduce product costs: Increase competitive advantage, expand market share.
Conclude
Vibrating feeders help increase productivity, reduce errors, and save costs. Automobile manufacturers need to invest to improve quality and optimize processes. SWOER specializes in designing and manufacturing vibrating feeders according to requirements. We are committed to providing effective, durable and accurate solutions.
Contact us
Please let us know your material size and required speed.