Vibrating bowl feeders, with their precise and efficient feeding capabilities, have become an indispensable solution in many industries. However, finding a vibrating bowl feeder that perfectly fits the specific production requirements of each business is sometimes difficult.
So why not design your own vibrating bowl feeder? What are the benefits? What steps does the design process involve? And what technical knowledge is needed to create a machine that works?
This article SWOER will provide you with a comprehensive guide on how to design a vibrating bowl feeder, from the basics to important considerations, helping you create your own optimal feeding solution.
Steps to design vibrating bowl feeder
Designing a vibrating bowl feeder is a complex process that requires specialized knowledge and experience. Here are the basic steps:
Step 1: Identify requirements
When selecting a feeding system, the following factors should be considered:
- Detail type: Identify the parts to be fed (electronic components, screws, bolts, etc.). Consider size, shape, weight, material and friction.
- Productivity: Determine the feed rate and volume to be processed to select a machine of appropriate size and capacity.
- Working environment: Consider temperature, humidity, and dust to select appropriate construction materials and protection levels.

Step 2: Design the vibrating bowl
- Shape: Choose the shape of the vibrating bowl suitable for the type of part and production requirements (round, linear, stepped).
- Size: Determine the size of the vibrating bowl (diameter, height) based on the size and number of parts to be fed.
- Spiral: Design the spiral with suitable pitch and pitch to ensure the moving part is stable and accurately oriented.
Step 3: Design the trap
- Trap Type: Select the appropriate trap type for the part type and classification requirements (gravity, mechanical, pneumatic).
- Operating structure: Design the trap's operating mechanism to ensure that only qualified parts pass through.
Step 4: Select the vibration generator
- Motor: Determine the motor type, power and vibration frequency suitable for the size of the vibrating bowl and the weight of the material.
- Spring and eccentric block: Select the appropriate spring and eccentric block to create effective vibration.
Step 5: Design the control system
- Controller: Select the controller (PLC, microcontroller) to control the machine operation.
- Human Machine Interface (HMI) design.
- Control interface: User-friendly control interface (HMI) design allows easy adjustment of parameters.
- Programming: Machine control programming, including functions to adjust vibration frequency, vibration amplitude, tilt angle, feed time, etc.

Step 6: Select materials and processing
- Material: Choose manufacturing materials that meet the requirements of durability, corrosion resistance, and hygiene (stainless steel, aluminum, plastic).
- Processing: Machining machine parts according to design drawings with high precision.
Step 7: Assembly and testing
- Assemble: Assemble the parts into a complete machine according to the correct procedure.
- Experiment: Test run the machine with actual material, check the operation of the components, adjust and calibrate until the desired effect is achieved.
Important factors when designing vibrating bowl feeders
Important factors when designing a vibrating bowl feeder:
- Material properties: Determine size, shape, weight, friction, adhesion to design vibrating bowl, trap and choose appropriate vibration frequency.
- Productivity & Accuracy: Balance between feeding speed and accuracy. Integrated sensors, vision systems to increase accuracy without reducing speed.
- Durability & Longevity: Choose durable, wear-resistant materials (stainless steel, aluminum, engineering plastics). Sturdy design, easy to maintain and replace.
- Safe: Ensure operator safety with cover, safety lock, emergency stop button. Avoid damaging parts during feeding process.
- Expense: Consider the cost of materials, processing, assembly. Ensure energy savings, reduce waste and optimize operating efficiency.
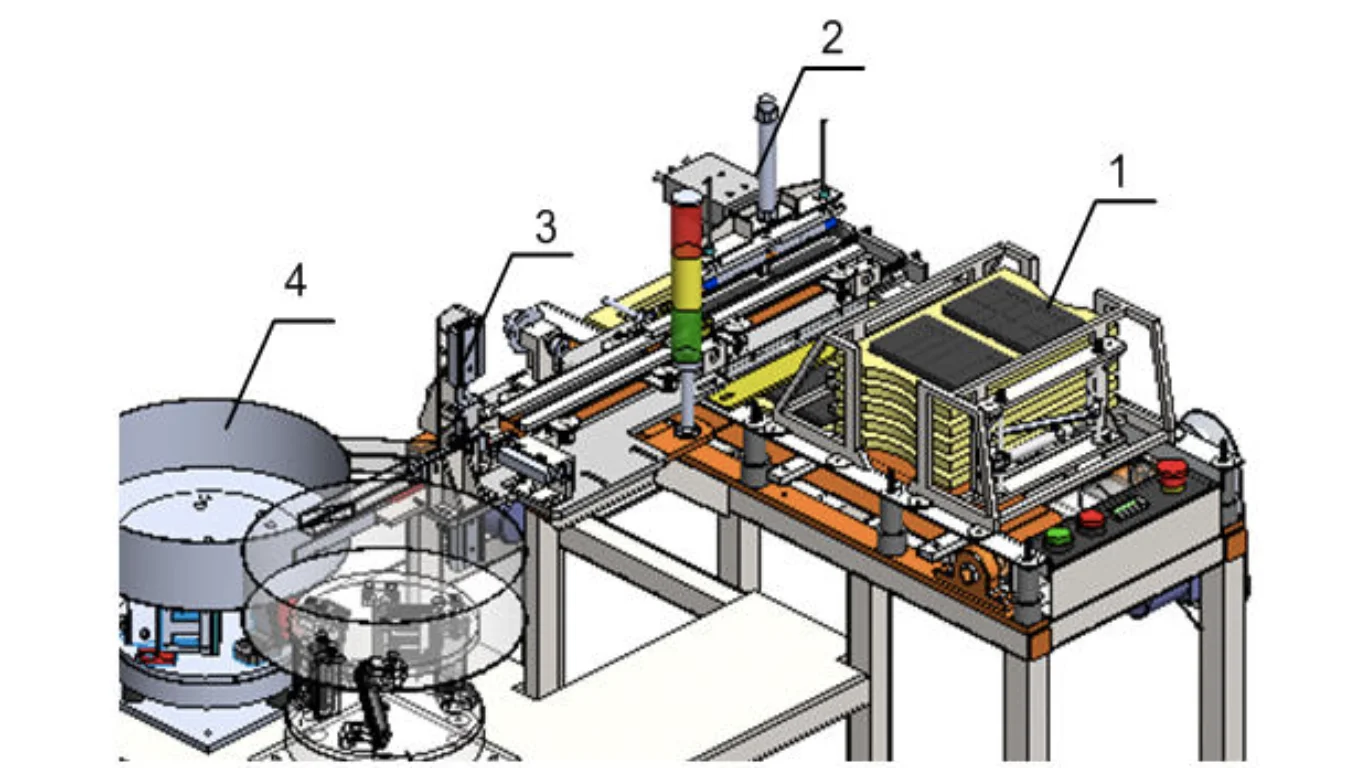
Design support software
Some popular vibrating bowl feeding machine design support software:
CAD/CAM software:
1. CAD (Computer-Aided Design) – Drawing design
CAD software helps to create 2D and 3D technical drawings of machines. Some popular software:
- SolidWorks: Easy to use, suitable for many industries.
- Autodesk Inventor: Integrated analysis and simulation features.
- CATIA: High-end, used in aviation, automobiles, ships.
- Solid Edge: Intuitive interface, suitable for small and medium businesses.
2. CAM (Computer-Aided Manufacturing) – Machining programming
CAM software supports CNC programming, creating detailed machining toolpaths:
- Mastercam: Most popular, supports many types of CNC machines.
- NX CAM: Integrates many advanced machining features.
- FeatureCAM: Easy to use, suitable for simple details.
3. Simulation software
- Motion simulation: Check material movement in vibrating bowl, optimize frequency, amplitude, tilt angle before manufacturing.
- Stress analysis: Evaluates the durability and deformation of machine parts under vibration, helping to increase equipment life.
Conclude
Vibrating bowl feeder design is a complex process, requiring a combination of professional knowledge, practical experience and a clear understanding of production needs. If you need advice on the design and manufacture of vibrating bowl feeding machines, SWOER ready to support. We provide optimal solutions with experienced engineers and advanced technology.
Contact us
Please let us know your material size and required speed.