In the era of technology 4.0, production automation plays a key role in improving productivity and efficiency. One of the indispensable equipment in modern production lines is the vibrating feeder. So what is a vibrating feeder? How does it work? What are the outstanding advantages compared to traditional feeding methods? And in which industries is it applied?
This article will answer all the above questions, and at the same time provide you with a detailed look at the operating principles, outstanding features and diverse applications of vibrating feeding hoppers. Let's join SWOER explore!
Operating principle of vibrating feeding hopper
Bowl feeders automatically sort parts from a random state into an orderly state by vibrating and guiding them along a spiral path within the bowl. Specially designed traps on the spiral path eliminate misaligned parts, ensuring that only correctly oriented parts reach the hopper outlet and continue into the production line. Each bowl feeder is individually designed, based on the characteristics of each type of part, to ensure optimal sorting efficiency.
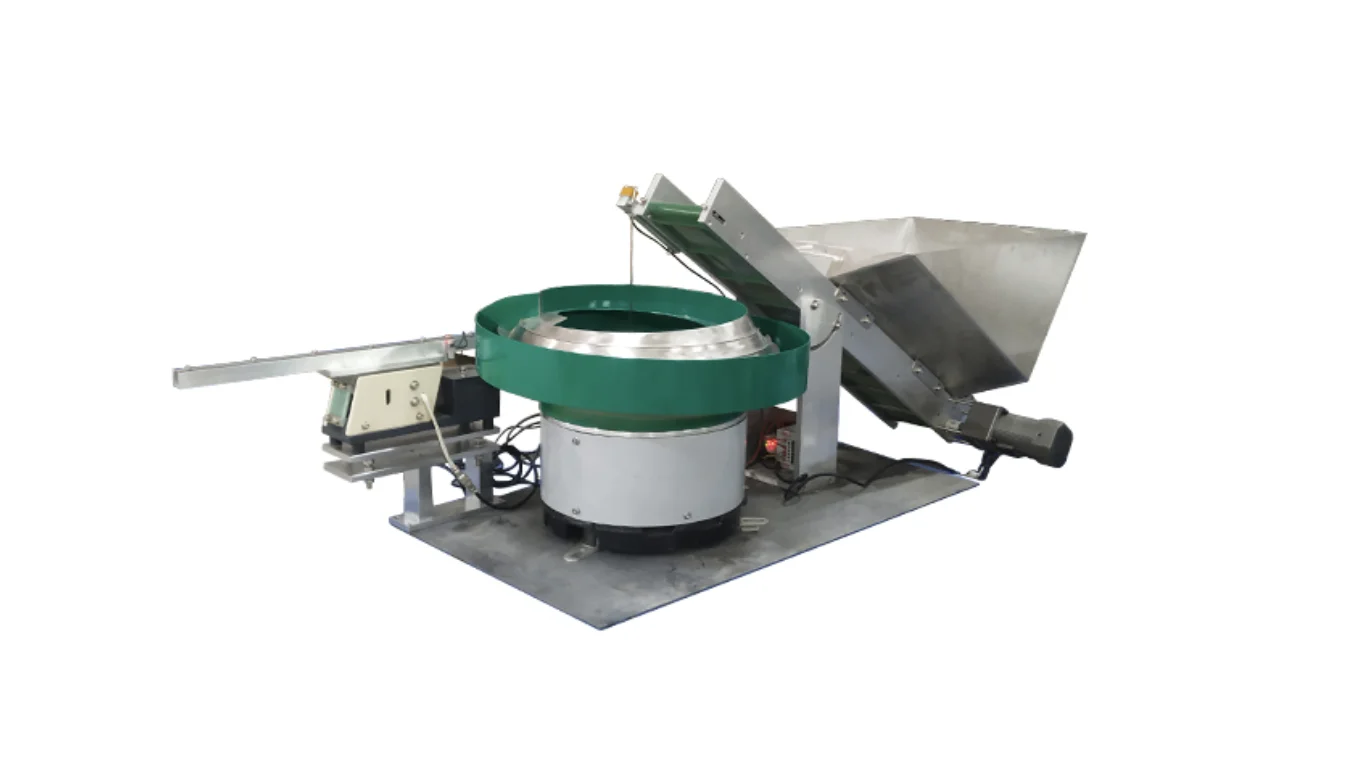
Vibration mechanism
- Create vibration: The bottom of the funnel is attached to a vibrating element. This element can be an electric motor with an eccentric block, or an electromagnet that creates vibration. When operating, this element will create mechanical oscillations, causing the funnel to vibrate.
- Impact on materials: Vibrations are transmitted from the bottom of the hopper to the walls of the hopper and spread to the material inside. This vibration force helps to “lift” the material and create movement. As a result, the material does not stick to the walls of the hopper and moves more easily.
Funnel shape
- Spiral form: Most vibrating feeders are designed with a spiral hopper cavity. This shape plays an important role in orienting and classifying materials.
- Orientation: When the hopper vibrates, the material moves in a spiral from top to bottom. During this process, the parts are oriented in a certain direction, which is convenient for feeding into the machine or the next stages.
- Classify: Combined with specially designed screens, grooves or traps, vibrating hoppers can classify materials by size, shape or other characteristics.
Feeding process
- Step 1: Material is fed into the hopper mouth.
- Step 2: Under the action of vibration, the material moves downward in a spiral path.
- Step 3: During transport, materials are oriented and classified (if necessary).
- Step 4: Finally, the material reaches the feeding point (usually a discharge port at the bottom of the hopper) and is fed into the next machine or process.
Features of vibrating feeding hopper
Vibrating feeding hopper has many outstanding features, bringing superior efficiency compared to traditional feeding methods.
Advantage:
- High productivity: Vibrating hopper has the ability to continuously feed at high speed, meeting large production needs.
- High precision: Materials are accurately oriented and sorted, minimizing errors and waste.
- Flexibility: Suitable for a wide variety of materials, sizes and shapes.
- Easy to operate and maintain: Simple structure, easy to use, convenient maintenance.
- Energy saving: Low power consumption, helping to reduce operating costs.
- Automation: Minimize human intervention, improve production efficiency.
- High durability: Withstand heavy loads, stable operation in industrial environments.
- Safe: Reduce the risk of work accidents.
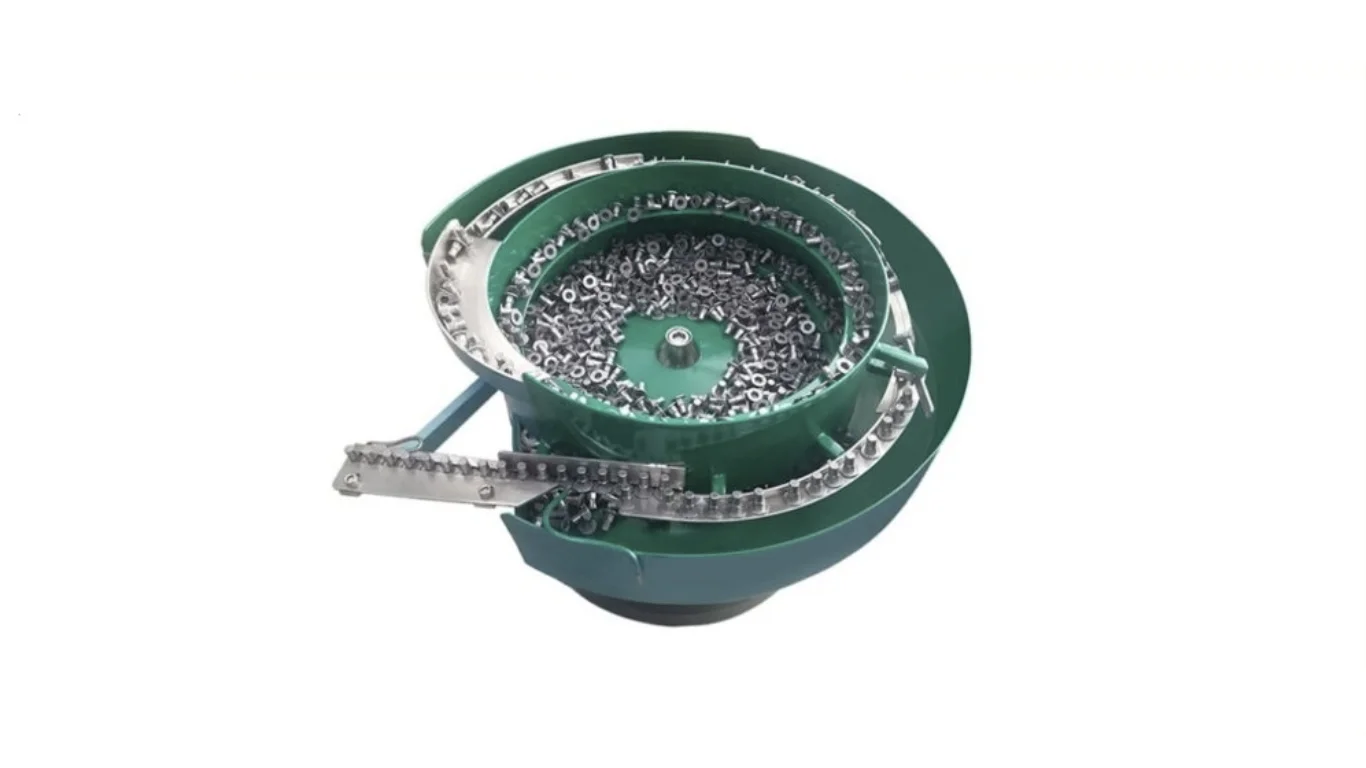
Disadvantages:
- Initial investment cost: Higher than some traditional feeding methods.
- Noise: During operation, vibrating hoppers can generate noise. However, manufacturers have improved to significantly reduce noise.
- Limitations with certain materials: Vibrating hoppers may not be suitable for materials that are too large, too heavy or fragile.
Application of vibrating feeding hopper
Vibrating feeder hoppers are widely used in many industries, automating production processes and bringing outstanding efficiency. Specifically:
Automobile manufacturing industry
- Application: Feeding small parts such as bolts, screws, nuts, etc. for assembly lines of engines, gearboxes, brake systems, etc.
- Benefit:
– Increase assembly speed.
– Minimize errors due to incorrect component supply.
– Improve labor productivity.
Electronics industry
- Application: Sorting and feeding electronic components such as chips, capacitors, resistors, etc. for production lines of electronic circuit boards, mobile phones, etc.
- Benefit:
– Ensure high precision during assembly.
– Minimize component damage.
– Improve product quality.
Food industry:
- Application: Feeding nuts, candies, cookies, etc. to automatic packaging lines.
- Benefit:
– Ensure food hygiene and safety.
– Increase packaging productivity.
– Reduce labor costs.
Pharmaceutical industry
- Application: Feeding tablets, capsules, etc. for packaging and labeling lines.
- Benefit:
– Ensure accuracy and hygiene during packaging.
– Avoid cross-contamination between drugs.
– Improve productivity and production efficiency.
Other industries:
- Household appliances manufacturing industry
- Machinery manufacturing industry
- Construction materials manufacturing industry
- …

Select vibrating feeding hopper
Choosing the right vibrating feeder for your production needs is important to ensure efficiency and cost optimization. Here are some factors to consider:
Material Type
Clearly define the characteristics of the material to be fed (granular, powder, block, size, weight, friction, adhesion, etc.). For example:
- Fragile materials require vibrating hoppers with low frequency and amplitude to avoid damage.
- Highly adhesive materials require a vibrating hopper with a non-stick coating.
Material size and shape
- Size: Choose a vibrating hopper that is the right size for the material size.
- Shape: Material shape affects the design of the flow path and trap in the hopper.
Required capacity
- Feed rate: Determine the feed rate required to meet production needs.
- Material volume: Estimate the volume of material to be fed in a given period of time.
Working environment
- Temperature: Choose a vibrating hopper that can withstand the ambient temperature of the working environment.
- Humidity: If the working environment has high humidity, it is necessary to choose a vibrating hopper made of anti-rust material.
- Dirt: If the working environment is dusty, it is necessary to choose a vibrating hopper with a sealed, dust-proof design.
Budget
- Investment costs: Determine the budget for purchasing a vibrating funnel.
- Operating costs: Consider the cost of electricity consumption and maintenance.
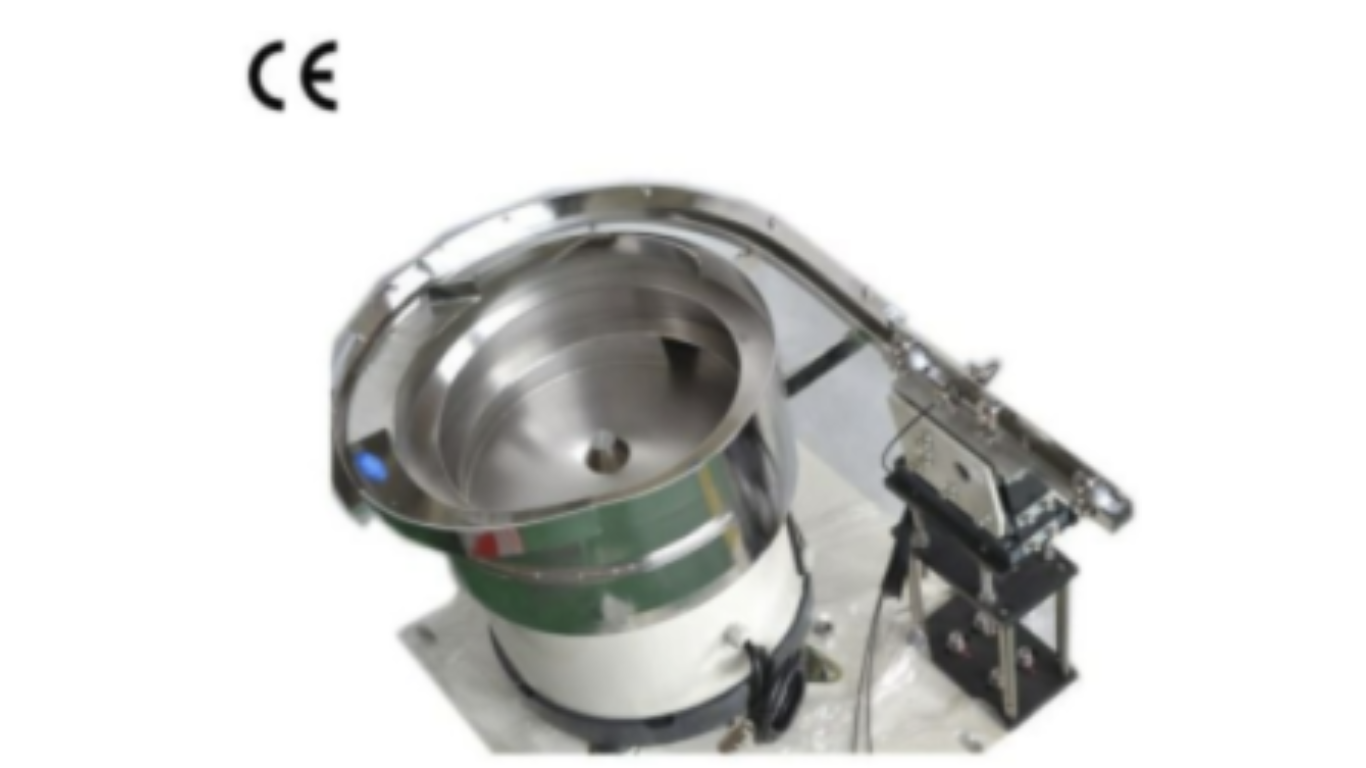
Advice:If possible, test the vibrating funnel with actual material before deciding to purchase. SWOER Providing a variety of high quality vibrating feeder hoppers to meet all customer needs. Contact us now for advice and the best quote! |
Vibrating hopper feeder is an effective automation solution, applying the principle of vibration to classify, orient and feed materials with high precision. With outstanding advantages such as high productivity, flexibility, easy operation and energy saving, vibrating hopper is widely used in many industries, from automobile manufacturing, electronics to food and pharmaceuticals. If you are looking for a solution to improve productivity, production efficiency and optimize costs, please contact us immediately. SWOER for advice and quotes on high quality vibrating feeder products!
Contact us
Please let us know your material size and required speed.